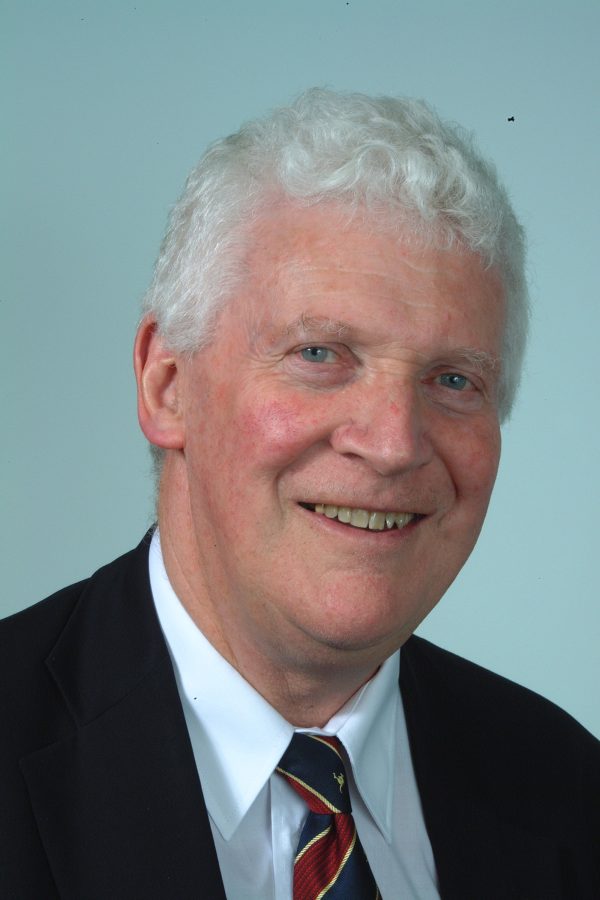
Prof Peter Dobson OBE was born during WWII in Liskeard, Cornwall and led a “net zero carbon existence” for his first 14 years without mains electricity or water.
After Grammar school, he chose a GPO (General Post Office, now BT) scholarship to take him to university and worked alongside Tommy Flowers. His broad career has covered a wide range of disciplines from physics and chemistry to materials science and engineering and bridged industry (Philips) and academia (Imperial College and Oxford). Peter was responsible for creating and building The Begbroke Science Park for Oxford University.
Peter has successfully spun-off numerous companies. His latest, Oxford NanoSystems was formed in 2012. He is currently on the advisory board of several companies involved in nano-materials, healthcare and energy. He was awarded the OBE in 2013 in recognition of his contributions to science and engineering.
Professor Peter Dobson OBE, was born in 1942 in Cornwall. His father was a teacher at a small village school and his mother taught domestic science on a part-time basis. He has a brother, Ben, who has a PhD in engineering. He says: “I grew up in Cornwall in fairly primitive conditions by our standards today. I lived in a house with no mains electricity, water, telephones, nothing, until I was fourteen years old. So I’ve seen what it’s like to be in what we would call nearly zero carbon conditions. I had to get all my homework done while it was daylight because at night we had no means of lighting to read by. It was a hard upbringing but my brother and I had a happy childhood. We really learned the value of learning and picking up as much science as we could at the time from our local library and our local schools.”
Peter attended his local schools. Speaking about his early influences, he says: “My dad was very keen on us learning about science because he’d been a navigator on a ship in the war. The local secondary school had some truly brilliant teachers. They were very motivational, especially in physics, chemistry and maths. The school itself backed on to the old gasworks in Newquay so we had practical demonstrations of chemistry actually in the gasworks. All of those things influenced me and even my art teacher influenced me because she was a brilliant artist and potter and she got us looking at the different minerals that went into pigments and glazes. All of this added up together and gave us a very well-rounded education.”
At the end of his formal schooling, with no prospect of a scholarship to go to university, Peter was encouraged by his physics teacher to apply for an apprenticeship with the General Post Office (GPO), now British Telecom. He says: “I applied for and got an apprenticeship and it was the best decision I made in my life at that stage, because the scholarship I won was worth much more than the scholarships awarded by the state to get into university, but it had the added bonus that it provided a lot of extra training.” Peter started his apprenticeship in 1961. The first year of his training included all aspects of telecommunications in London and his local region and vacations spent working for the GPO. He says of the experience: “Some of it was grim. I was put into accommodation in a very rough part of London and coming from a very rural part of Cornwall I found that quite a severe shock. I would try to get away at weekends back home to Cornwall as often as I could because I hated London at that time. “I was working most at that time in the headquarters of the General Post Office in the City and it was really boring, horrible work in my view, I didn’t enjoy it at all. It started to get much better during the winter when I was transferred to some of the research and development activities and one of the activities I enjoyed the most was in one of the most beautiful houses overlooking Regent’s Park. “The GPO had laboratories in the basement of Regent’s Park Terraces and this was a really exciting period, these guys were all backroom boys left over from World War Two who were used to inventing things. I learned all about things like electrostatic spraying, ultrasonic cleaning, and then I went on to apply that in the factories that were run by the GPO. “For example, in the factory in South Wales we applied the lessons of ultrasonic cleaning to cleaning up those old telephone dials. They used to dismantle them and brush them and put them back together, but we found we could just dunk them into a bath in an ultrasonic cleaner and they came out as good as new. So there were little things like that which made my life really exciting and all the time I was trying to learn more, it was the right environment for me.” While working at Dollis Hill, Peter was assigned a mentor. He says: “I first met and talked to Tommy Flowers at Dollis Hill and then I was assigned to one of his colleagues, Albert Lynch who was a very tall, commanding, eccentric individual. The thing I admired about him most was he had a very old Rolls-Royce which he drove up to the laboratories. … All of the people that I met in Dollis Hill and in Regent’s Park Terrace were very, very nice human individuals and I cannot fault them, they were all great.” Of Tommy Flowers, Peter says: “At the time I just thought this is just the sort of person one would expect to be in a leading research laboratory. I knew very little at the time about Colossus, in fact nobody did, he didn’t talk about Colossus. What was spoken to us was about the possibilities of using the technology that was used in computing machines, as he put it, to run a telephone exchange. Ultimately that did lead to the creation of the first electronic telephone exchange at Highgate which did not use valves but was based on transistors. I think everybody had realised that valves were too unreliable to really do a telephone exchange job properly and you’d have to get the smaller, less power-hungry transistors to do that. It was a really interesting transition time when we were trying to get rid of valves and bring in transistors. “In Dollis Hill there was still a lot of activity in what we called special quality valves, because we didn’t see how we could put transistors into repeater stations and the trans-oceanic cables. It was in the fourth year of my apprenticeship I had a very nice time working on high quality, special quality valves which you could put into a repeater, pop it down on the seabed and it would last for 15 years. This taught me a lot about surface science, especially surface physics, to design the cathode of the valve and it led to me leaving the GPO and doing a PhD in that subject, with the long-term intention of coming back to the GPO or working closely with them.”
Having learned a little about surface science and physics, Peter decided to leave the GPO to study the subject at Southampton University, a place he chose because it was close to the sea. He intended to return to the GPO after his studies, however, upon completing his undergraduate course, he chose to stay Southampton to do a PhD in ‘Epitaxial Growth of Thin Films of Metals’. He says: “At Southampton I messed about a lot, I played a lot of sport and things like that, got involved in the various music scenes, met my future wife while I was there. At the end of my undergraduate time when I was wondering whether to go and work on a cable ship for the GPO or do a PhD, the PhD won out because I was getting married and I wanted to stay on dry land rather than on a cable ship. I did surface physics, partly with a view to trying to make radio valves more reliable, but I very quickly switched into growing semiconductors and metal films. I did quite a lot of epitaxy, growing a single crystal of a metal film on top of a single crystal. That work really dominated the next 20 years of my life.” Peter says that if it had not been for his wife supporting him financially he would not have been able to complete his PhD. He adds: “At the time, she was a computer programmer assistant engineer in Southampton. She carried on that career after she had our kids and she worked for ICL, which was later bought by Fujitsu. She was one of the pioneers of the homeworking schemes that ICL developed when they realised there were lots of women who’d had families and were tied to home, so as soon as the technology permitted, ICL started to install computer terminals. In the early days it was a Texas Silent Writer terminal at home, later on it was a video monitor. At one time, my wife had a team of homeworkers who were under her direction all doing the programming work from home. She enjoyed that and she carried on working in computer support and working from home until she retired two years ago.”
After completing his PhD, Peter was offered a lectureship at Imperial College where he stayed for sixteen years. Peter maintained contact with the GPO throughout his time at both Southampton and Imperial, keeping up with developments, obtaining research funding for his students and interchanging ideas. He says: “I took the work I’d been doing at Southampton with me to Imperial College. I did a lot of electron diffraction of epitaxy, as we now call it. Still concentrating on metals, and it was over a period of that sixteen years that I got back into the semiconductor field. Even well-found laboratories such as Bell Labs, Philips and IBM found that the semiconductor growth needed to have much more sophisticated manufacturing systems and in particular a technique we now call molecular beam epitaxy.”
It was while Peter was recuperating from a period of illness that a colleague at Philips asked him to bring his understanding of electron diffraction to help them interpret some pictures. He says: “I found that we were able to study how a semiconductor crystal grew and formed a single crystal.” It was after this experience that Peter moved to Philips. He explains: “It was a tapered move, I’d had a year of part leave of absence and then I moved completely and became a permanent employee at Philips.” The culture at Philips has made a lasting impression on Peter as he describes: “Working for Philips was terrific fun. They had a very, very flat structure. There was no pyramid hierarchical thing about it and everyone felt they could contribute to an invention or to what the company was doing. I found that really exciting and it’s a thing which has stayed with me forever. When I became a director of the laboratory later on in Oxford I made sure that I went round and met as many people in the facility as possible and really talked to them about what they were doing, why they were doing it and what they wanted to get out of the job. That was the sort of atmosphere that went on in Philips and it’s stayed with me. Looking back on it, it was quite similar to Dollis Hill in many respects, but Philips took it much further because they’re a commercial inventive company and I think that’s how Philips invented so many things. They just allowed every worker to feel they were contributing to the good of the company.” While working for Philips, Peter had the opportunity to visit its headquarters in Eindhoven on several occasions to work collaboratively. Having worked in semiconductor growth for many years and solving many of the problems associated with it, Peter then got interested in new devices and moved into a new lab. He adds: “At first I operated in a lab where I was making measurements for other people in the building who were growing semiconductor layers for lasers. While I was doing the characterisation I was able to experiment with things like modulators for light in semiconductors. It was a bit restricted because it had to be geared towards the business side of Philips and I wanted to diversify. I wanted to see if we could use light for computing, for example. I also wanted to see if we could use these laser diode structures made as simple light emitting diodes to emit light for lighting.” Peter explains that because Philips kept its lighting and semiconductor divisions separate, his interest was not particularly encouraged at that time.
Peter next moved on to the University of Oxford only to find that the department had forgotten he was coming. He says: “They wondered who I was and what was I doing there. I was put in a really uncomfortable position of having no laboratory, no office and I had to give up on bringing all the optical equipment that I’d planned to bring from Philips into Oxford because there wasn’t anywhere to put it. “I was stuck wondering what to do. I decided to look at something called quantum dots, which are what happens if you shrink a semiconductor down in all three dimensions. When we made the lasers in Philips for the CD players and DVD players we effectively shrunk the dimensions down so there were very thin layers, quantum well layers, and that’s what the quantum well laser is all about. To this day they’re very, very successful, they’re in everybody’s disc reader. “I wondered whether we could do this by making tiny particles of semiconductors and pump them and create light or lasing. I wanted to do a different approach altogether, I wanted to use wet chemistry.” This was a technique that he had done at Philips in his spare time and knew it was possible. He continues: “In Oxford I set up a lab to do a lot of it and I started to grow semiconductor particles which showed really interesting light emitting properties and later this led to forming a company called Oxonica. In the meantimea chemist called Professor Allen Hill was in my college and he saw that I had some of the skills that were needed to make biosensors and he got me interested in making enzyme directed biosensors. Allen Hill had already invented the glucose sensor which has transformed the lives of diabetics and that was already coming on to the market through a company he’d help set up called MediSense. I became an unofficial consultant to them. Then we started to make new types of sensors which would do other things such as measure things like lactate, and some of the compounds that give you an idea whether you were going to have a heart attack, and assess for cardiac risk. ” In 2000, the pair formed a company based on this work called Oxford Biosensors. It was this introduction to biosensing that saw Peter work on some of the early DNA sequencing machines with Professor Ed Southern in the Department of Biochemistry. He adds: “So Oxford’s inability to give me a laboratory from day one turned out to be an advantage because it got me collaborating with two really brilliant people in the bio area. I had to think of what could I do with minimum facilities in the semiconductor area, and that’s what led me to making quantum dots and nanoparticles. So all was not lost.”
Peter became involved with a spin out company called Opsys which was founded in collaboration with the Chemistry Department at the University of Oxford. He explains: “My postdoc was working on quantum dots and the chemistry student was working with rare earth compounds which emitted light. It was a sort of competition to find out which is the best technology: the rare earth compound or the quantum dot. Even to this day I’m not sure which is the best, but these two guys decided to work together rather than fight each other to see what they could do with the rare earth. “The rare earth compounds were certainly easier to make in terms of getting the three important colours, red, green and blue. We were able to synthesise a range of these compounds and they emitted light at the corners of the chromaticity diagram, so they gave a very good, sharp, crisp image when the light was combined. They found they could make these compounds so that you could put them down using wet chemistry, or you could go into vacuum chemistry and evaporate them. I was really amazed at the crispness of the colours they were achieving from these.” While Peter decided not to get involved with running the company, he provided lab facilities for them. By 2002, they were making full colour displays of mobile phone sizes. Unfortunately, their investor, 3i, pulled out, and the company was sold to a rival company Cambridge Display Technology who broke it up. Peter adds: “The entire Opsys technology was lost and broken up. It’s a great shame. You can see how successful it was because a lot of those ideas were taken over to Korea and ended up in places like Samsung and LG. We had employed quite a lot of Koreans in the early stage, partly because we couldn’t find any homegrown skilled technologists to make the things. “This is a problem here today. There are lots of the great ideas coming out of British universities but we don’t have enough people at the highly skilled technician level to turn these into commercial reality. It’s a lesson that Britain hasn’t learnt. It was tragic, I think we could have had a really powerful display industry if we’d managed to keep that company alive.”
In 1999, Peter formed another spin-out company called Oxonica working in nanotechnologies. The company looked at a number of systems. The first was particles for the display industry which they trialed with Motorola and Sony and others, but they were ultimately rejected. However, they then found that the titanium dioxide they had made for another application was very good for a sunscreen. It not only blocked ultraviolet light, but also acted as a very good scavenger of free radicals. Boots the chemist’s trialled it, approved it and started selling it. The process took two to three years. Peter says: “It broke the rules of innovation which normally takes ten to fifteen years, we had actually got something out there in three or four years.” The company then turned their attention to nano cerium oxide to help burn oil in diesel engines. The work was the result of a conversation with an inventor who had initially discovered that adding cerium oxide to diesel fuel stopped blue smoke but unfortunately, its abrasive qualities eroded the engine. Peter says: “A team of our people in Oxonica developed nano cerium oxide and we found a way of making the material which was a really good catalyst to help burn all the oil in the engine during the explosion. If you put our stuff in the fuel we didn’t get any smoke coming out the tailpipe and we got more efficiency. This was trialled in buses in Hong Kong in 2003 and it was a great success. The bus companies liked it because it gave them better fuel efficiency.” The product was also trialed in the UK after Stagecoach brought the Hong Kong bus company. Peter says: “For many years we had an exclusive contract with Stagecoach and this lasted until about two years ago when the diesel engines of the latest variety are so good in terms of their efficiency, they’re not improved by putting in our additive. A lot of inventions are like that, they get a window of opportunity of about 15 years and then it goes off.” The experience taught Peter and his team that you need the “pull of the market.” Peter goes on to say that Oxonica lost its way, adding: “They ended up satisfying their shareholders by downsizing, selling off lots of stuff and the story ended there. The fuel additive carried on as a separate company that was bought out. The sun cream has just survived on royalties and the patent ran out last year, so we’re now looking for new things.”
In 2002 Peter became the Academic Director of the Oxford University Begbroke Science Park, a role he held until September 2013. Peter explains: “I got the job of running the Science Park. It was a risk on my part because I was still keen on research and teaching, but I thought there’s not many other people in the university who are qualified to do this, but I’d seen companies grow and die. All the companies I had up till then were growing and growing very successfully, so I got the job in 2002. I had to relinquish my teaching fellowship in Queen’s and also all of the teaching that I did in the department. My role then was to try and raise the money to develop the site and it was quite tricky. “The vice-chancellor and the team at the top of the university liked the idea but didn’t have a clue how to grow the site. I knew how to grow it, but didn’t know how to get the permissions and the money. I learned how to form relationships with local politicians at both the city and the county level and then at the bigger regional, south-east regional level. We got quite generous support from the South East England Development Agency and we were able to get money together to build buildings. As soon as that started to happen, the university saw the merit of this and started putting extra money in to actually equip the buildings and furnish them.” As a result, Peter built a small team and ran a planned continuous development of building on the site. He adds: “At the same time, I kept an open-door policy for academics in the university who wanted to come and talk to me about spinning off companies, and for all the companies that were moving on to the site and wanted advice. It just worked. I think it was helped a little bit by having the Materials Department characterisation service sited on the place. We had electron microscopes and lots of analytical gear on-site which small companies could hire or rent time on, and that worked really well. I think there was an element of luck about it, but you’ve also got to go and put effort into making sure that the luck works for you, and that’s what I did. It was almost like a very enjoyable hobby but it consumed huge amounts of time.”
Around 2012, Peter and a friend, Mark Evans, an accountant, with whom Peter had spent two days teaching MBA students, decided to see if they could set up a company. Peter explains: “We were sat in my office talking about the two days that had just gone past and he said ‘do you think we could start up a company, a real company, just off an idea that we have here sitting talking’. We looked at some copper structures that were sitting on my bookcase and he asked what they were for. I explained that they could be used for heat exchangers if we could make the surface in the right way. We then decided to put them in an MBA proposal for a team of students to convert a copper sheet into a heat exchanger. “It was a realty wacky idea but we did it and we got a team who put the idea forward in the business plan competition and they actually won. A bloke in the audience came up with £300,000, which really surprised me, because there was no experimental data at that point to say that it could be done, and all four of the team were non-scientists. “I was scratching my head and thinking, wow, what are we going to do here. We decided to risk it, it wasn’t our money after all, it was an investor.” At the same time, a friend asked if Peter could help find a job in Oxford for his son, Alex Reip, a physicist from Brunel University. Peter says: “I offered him a role as a chief technical officer of a company that doesn’t really exist yet, but if he works at it, maybe it’ll work.” Three of the winning MBA team dropped out, however, we found a way of treating surfaces of anything and turning them into very efficient heat exchangers. Peter adds: “This was in 2012/2013 and already we could see that if you were going to solve climate change in the long run you’re going to have to make things like heat transfer much more efficient. So, we thought this could be a bandwagon that will roll and roll forever. We started to get money in to grow the company. Unfortunately, the investor didn’t want to put any more money in, in fact, he really wanted to take his money out at a profit as soon as possible!. , But we stuck at it, we got a lot of the government grants and kept the company alive and growing during that period. After four years, five years, we were certain that we had created a surface which improved heat exchange by a factor of between three and five times. Then came the crunch, can we apply that to a real system, a heat pump, a refrigerator, heat pipes and things like that? and that’s where the progress has slowed down. When you start taking these things out of the lab and putting them into real systems, the improvements are nowhere near as big as the ones you measured under ideal conditions and that’s where we’re at now.” It’s a challenge we are hoping to solve With time and money running out, Peter and his team are ‘pivoting’ as he explains: “We’ve suddenly found these surfaces are brilliant as electrolysers to generate hydrogen and one of the students working in the company has shown with his colleague that these same surfaces we were using for heat exchangers are brilliant at creating hydrogen in electrolysers. So, we’re pivoting into a different application. It’s a pretty exciting period, because hydrogen is in great demand, again for “net zero”. At the moment, the only sensible way of storing energy from excess wind or a solar energy is by converting it into hydrogen and then storing it in tanks or underground, I don’t think batteries will ever satisfy the huge capacity needed.. So we’re sitting on two possible applications and we really need much more capital investment than we can get easily at the moment. “We’re in a country where we have a Prime Minister who boasts about world beating this and world breaking that, and yet they’re not prepared to put their hand in their pocket and help the companies that are trying to do it and we’re feeling very frustrated.”
After leaving Begbroke, Peter was invited by Lord Bhattacharyya to join Warwick Manufacturing Group. Peter says: “I was invited to work as much or as little as I liked, Lord Bhattacharyya gave me a completely open-ended deal. I didn’t want to go there five days a week, but one or two days a week would be fine for me and that opened up so many doors.” Alongside the offer from Warwick Manufacturing Group, Peter was also offered a visiting professorship at UCL in chemical engineering, a visiting professorship in King’s, in physics, later translated into engineering. He also taught at Bristol and was appointed head of their Industrial Advisory Board, plus a role at Birmingham University, chairing their facility for nanotechnology in the environment. He says: “These really filled my days and more, some days were quite bizarre: I’d be in a different town each day of the week. It was beginning to get quite tough until I realised that I could actually pull back on this.”
Of the key decisions taken throughout his career, Peter says that his father’s advice to go into science was the first he took, followed by his apprenticeship with the GPO which “opened my eyes up to the way that science, as taught at advanced level in schools, is applied in the real world.”, He says of his move into academia: “I quickly realised that I was quite good at teaching and putting across research ideas and what mattered in terms of the science to an audience, so it was natural to be a university lecturer. It sounds arrogant, but I was quite good at it and I got a lectureship in the third year of my PhD studies, which was unheard of, I really did have the way of putting stuff across.” The next big turning point for Peter was joining Philips and understanding how a well run company can lead to invention. He adds: “That taught me a lot about not being selfish and worrying about your own personal career, but worrying more about the social implications of what you and your team were doing and how to get it out there for the benefit of everyone. That really cemented in my mind that the best thing in life is to help others, and that’s been my guiding thing from then onwards.”
Asked what the relationship should be between academia, research and industry, Peter says: “The way that academia and industry should work is much more with a partnership where there’s more sharing of people. Bringing people from industry into the university in some capacity to help, but also having the facility where you can go out and work in a company for a short period. It’s much better to be able do it for two or three days a week, but geographically that’s not always possible, but the short periods are best because you can get a freshness for the information transfer when you’re going from the company back into the university and vice-versa, there’s this immediacy with it.”
“There was still a lot of work to be done to convince people in industry that there was merit in doing more with nanotechnology and there was also merit in getting people from the academic side to see it much more closely from the industrial side. “I think that there’s an enormous amount of money in Europe that has been wasted – and I mean really wasted – on nanotechnology. They’re obsessed with nanotechnology safety. Quite frankly, they’ve made up most of the danger aspects! There is some risk, but there are no huge dangers in nanotechnology as a technology. However, the European Union has funded more grants on nano safety than it has on nano innovation, and I think that’s shameful. If you look at America and China, it’s completely different. Both of those countries are forging ahead, applying nanotechnology to just about everything. In Europe we’re lagging behind because of this obsession with nano safety.” On the future of healthcare, Peter says: “Healthcare’s very closely linked to the safety issue. In healthcare what you’re trying to do very often is to get nanoparticles into the body. The safety people say, ooh, they get in all the time, but they don’t. It’s quite hard to target a nanoparticle into the body in the right place at the right time. If you can do it, it can have tremendous beneficial effects. You could reduce the drug loading so you’d reduce a lot of side effects if you can target a nanoparticle containing a drug into the right part of the body, or if you can get the nano diagnostic to improve the sharpness of an MRI image. There’s a lot of work to be done and I’m really heartened by the work that’s been done by the vaccine companies, some from Oxford. Moderna and Pfizer-BioNTech are using nanoliposome technology to deliver their mRNA drug. Until two years ago, in my lectures I was saying this is still quite a long way off before we routinely use this, but it’s been used, tried and found very, very successful and already we’re beginning to ask the questions if this liposome encapsulation is going to be useful for lots of other diseases and so on. Nanotechnology’s really going to play a very important role in treating disease and everything from the brain, cancer right down to mitochondrial diseases in humans. The sky’s the limit at the moment for applying nanotechnology to healthcare and medicine.” Peter is working on a project with University College with his friend and colleague, Rachel McKendry, who is leading the i-sense infectious disease sensing programme there. It is a joint project with Imperial. Peter says: “Some of the work that they’re doing there is really showing the way to future infectious disease detection, both for microbes and viruses. It’s one of the great pleasures of my life to be associated with it.”
Asked about what advice he’d offer people thinking of going into a career in nanotechnology, academia or research today, Peter says: “Never be worried about when you get to a decision point, just go with your best instinct and do what you think is right, and usually that means something which is going to make you satisfied and happy.” Describing himself as an interview panellist from hell, he adds: “I want to find out what makes people really tick and how they’re going to become good citizens in the future and that’s why I say people should think of doing things from a gut instinct, when they’ve got a decision to make, make it from the point of view of the big scheme of things and not just for your personal selfish objectives”
Interviewed by Elisabetta Mori
Transcribed by Susan Nicholls
Abstracted by Lynda Feeley